Projekt: GreenHiTemp
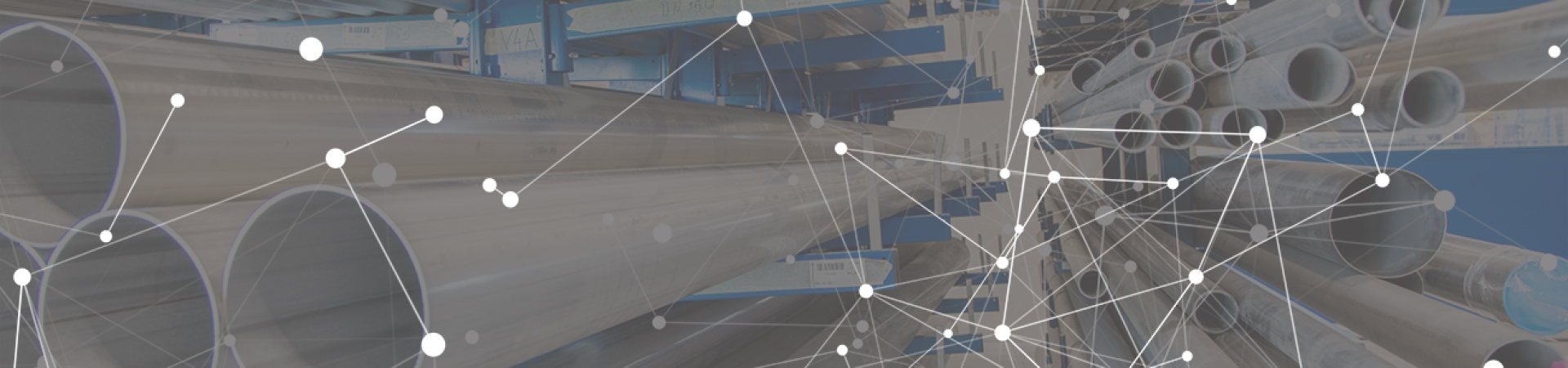
Entwicklung eines Grünen Digitalen Zwillings für dynamische, hochtemperierte Fertigungsprozesse zur Steigerung der Ressourceneffizienz (GreenHiTemp)
Deutschland ist Technologieführer in der Massivumformung und weltweit zweitgrößter Produzent massivumgeformter Bauteile. Geschmiedete Teile sind oft sicherheitsrelevante Bauteile, die eine 100 %-Qualitätskontrolle erfordern. Diese erfolgt bisher nach der Umformung Stunden später nach Abkühlung des Bauteils mit berührend messenden Sensoren, da herkömmliche optische Prüfverfahren an glühenden Bauteilen an ihre Grenzen stoßen. Wird im Nachgang ein Fehler festgestellt, müssen ganze Chargen von Fertigteilen eingeschmolzen und neu produziert werden. Daraus resultieren neben einem hohen wirtschaftlichen Schaden je Bauteil auch große zusätzliche Energie- und Umweltlasten.
Hier setzt das Vorhaben an, indem es eine 100 % Inline-Qualitätskontrolle der heißen Bauteile sofort nach der Umformung und eine aus der Qualitätsprüfung abgeleitete korrigierende Prozessregelung verfolgt. Dazu werden prozessintegriert die Qualitätsparameter erfasst und in einen digitalen Zwilling eingespeist. Auf Basis selbstlernender Algorithmen sollen Prozessanomalien frühzeitig erkannt und die Produktion durch gezielte Stelleingriffe optimiert werden. Dabei sind die harschen Randbedingungen in der Warmumformung (Dämpfe, glühende Bauteile, Vibrationen) zu beherrschen, indem robuste thermografische, optische und radargestützte Sensorik eingebunden wird. Es ist mit der Reduzierung der Ausschussquote von etwa 80 % zu rechnen, womit für Schmieden mittlerer Größe Einsparungen von 100.000 Euro pro Jahr realistisch sind. Zusätzliche Einsparungen ergeben sich für Material, Energie bzw. CO2-Emissionen, womit GreenHiTemp einen entscheidenden Beitrag zum Klimaschutz durch die digitale, grüne Transformation der Wertschöpfungskette in einem energieintensiven Produktionsbereich leistet.
Die Erschließung des neuen Marktsegments „Digitales Gesamtsystem zum Messen und Regeln in der Warmmassivumformung“ lässt sich zudem auf die weiteren deutschen Unternehmen der Branche mit ca. 80.000 Beschäftigten übertragen. Als zweiter Anwendungsfall für den Digitalen Zwilling wird die inlinefähige Qualitätskontrolle beim Presshärten durch den Einsatz von Infrarottechnik entwickelt und validiert. Auch in diesem Wachstumssektor sind große Energie- und CO2-Einsparungen durch die 100 %-Kontrolle zu erwarten.